YOU MAY ALSO BE INTERESTED IN…


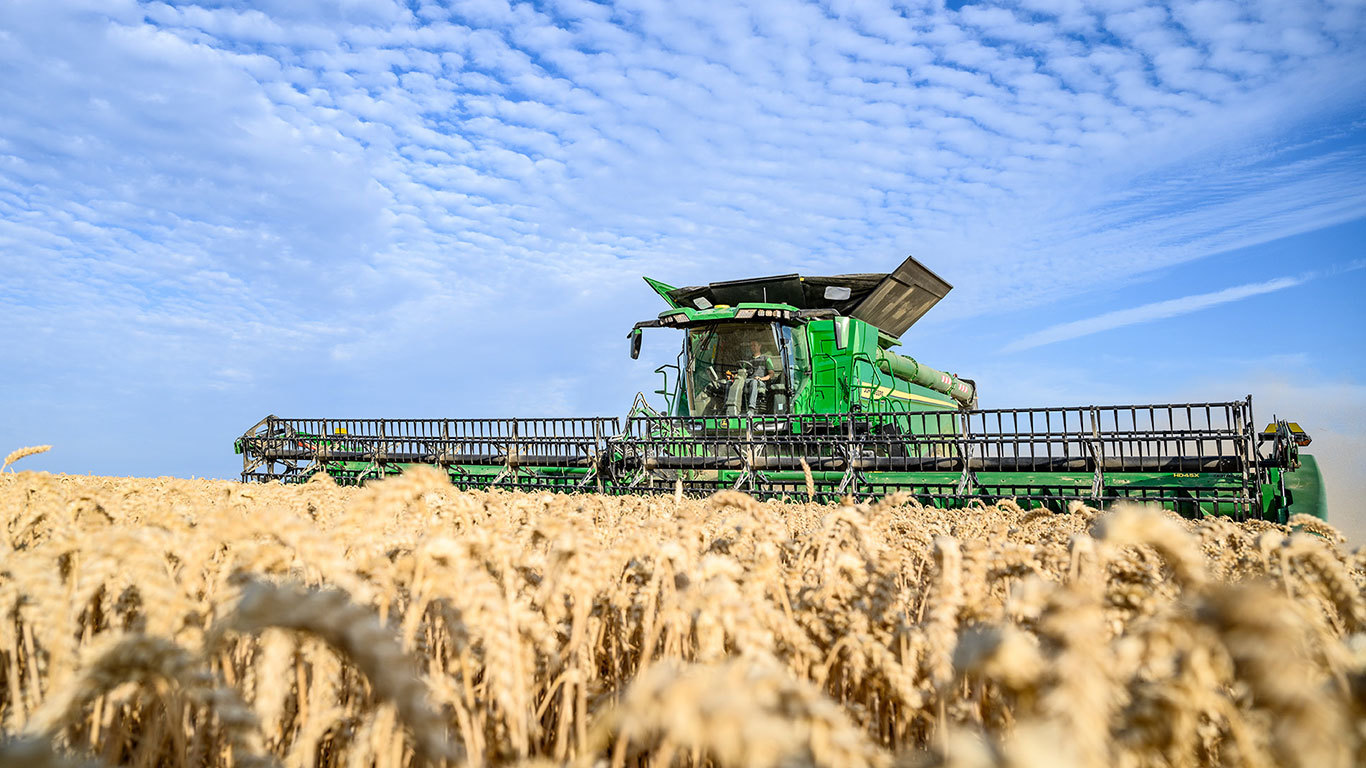





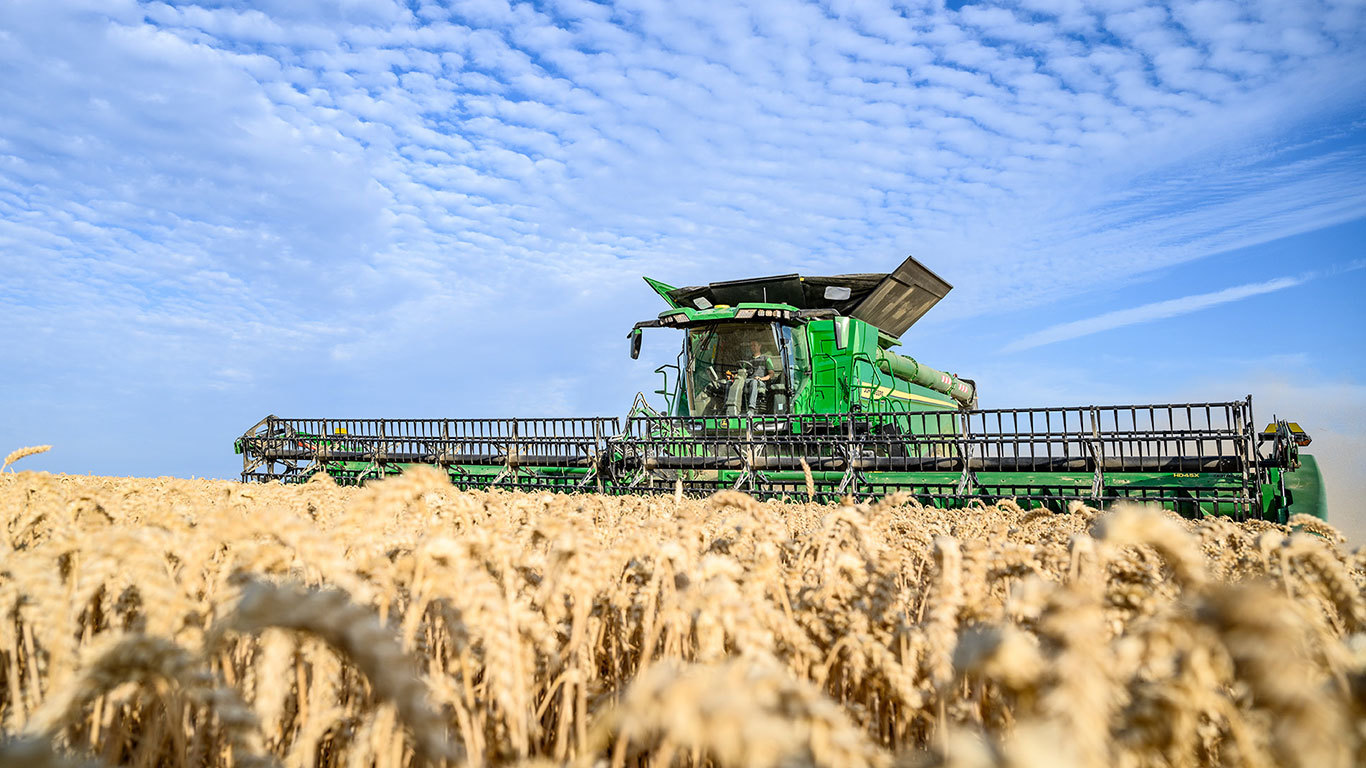



X9 1000 Combine
- 100 t/h massive Throughput with 13.70 m Super-wide cut header
- 1,720 mm channel width and 4.00 m² effective Threshing Area
- Effective Rotor Separation area: 22.50 m²
- Total cleaning shoe area: 7.00 m²
- 13.6 l Engine, 470 kW/639 hp max Power

X9. The 100 Tonne Combine
- 100t/h - Massive Throughput
- 13.7m - Super-Wide Cut
- < 1% - Broken Kernels
- 14h - Fuel Tank Capacity
- Harvest Promise – Uptime Guaranteed
- NEW CAB - Quietest ever
- Combine Advisor - Stress-Free-Automation
- JDLink - Mobile Connectivity
- DataConnect - Data Sharing
- Operations Center - Digital Farm Management
Combines X9-Series





































Related Products
Features
Collapse All
Expand All
Ultra-efficient crop feeding with headers to match the combine
Catches every grain
John Deere’s updated range of Hinged Draper (HD) headers were developed to match the X9 Combine’s huge throughput. They follow the ground like no other header, catching all the grain and reducing tillage costs.
High throughput

Crop is delivered headfirst into the feeder house for more efficient loading and separating. Draper belts are also unaffected by the moisture content of the air or crop. This allows operators to harvest more efficiently at the start or end of the day when moisture levels are higher.
- 15.2-m (50-ft) super-wide cut
- 1200-mm (47.2-in.) extra-wide belts
- 2620-mm (103.1-in.) total wing range
The belts feature a patented ridge pattern design that’s unique to John Deere. This traps small grains like rapeseed and prevents them from rolling off the belt and back into the field. The design also removes the need for additional grain saver systems like air blowers, which increase the weight, power consumption, and maintenance requirements of the header.
Unmatched ground following

The hydraulically adjustable attachment frame moves vertically, which helps isolate the combine from the header for better ground following.
The header wings behave like two independent cutterbars. Flexing by up to 10 degrees, they deliver great performance in down crop and leave even stubble on irregular ground. Together with the attachment frame, the vertical movement at the wing tips is 2620-mm (103.1-in.) on the HD40X. A tight reel-to-cutterbar distance is also maintained across the full width, thanks to the projected pivot point of each wing meeting in the centre of the header.
Harvest more crop quickly with the heavy-duty feeder house
Massive capacity
The wider, longer, and stronger X9 Combine feeder house lets you harvest faster in high yielding crops.
Handles the largest headers

Your combine capacity won’t be constrained by header size. The X9 will easily handle 18-row corn heads or larger and 15-m (49-ft) or larger small-grain headers.
- 45 percent more volume
- 6150-kg (13,558.4-lb) lift capacity as standard
- 950-Nm (700.7-lb-ft) slip clutch
Excellent terrain following
The independent frame connecting the header to the feeder house isolates the header movements from the combine.
High field speeds
With 1300-mm (51.2-in.) lift height, you’ll have no problem picking up or dropping off a header on a trailer, even on uneven ground. It also lets you drive over obstacles and move from field to field without removing the header.
Easy header connection
Travel across fields to the next patch at speeds of up to 20 km/h (12.7 mph) with a large header attached thanks to the heavy-duty construction and high torsional rigidity.
Automatic feeder house cylinder lockout
The feeder house is automatically locked as soon as you leave the seat. The header can also be locked at any height for easy maintenance (e.g., when changing a stone-damaged knife).
Improved crop flow with eight-wing chevron feed accelerator and stone trap (FAST)
Low-energy crop transition
The crop flow from the feeder house to the rotors has been streamlined to reduce friction and increase efficiency.
270-degree feeding vanes

In all rotor combines, the transition from tangential to axial crop flow is a potential pinch point that can consume considerable power. One of the major design innovations of the X9 Combine is the eight-wing chevron FAST, which enables a very energy efficient crop flow transition.
As the crop mat emerges from the feeder house, the stalks are perfectly aligned thanks to the headfirst draper feeding. Once it reaches the FAST, the central chevron vanes start to evenly divide the crop mat into two separate streams. A divider between the two rotors further smooths the crop path towards the rotors. The space between the FAST and the tips of the rotors allows the crop to gently expand before being drawn into the 270-degree feeding vanes. This extra space also contributes to the huge throughput of the X9 as the crop is less constrained and the wide body can handle large volumes without overloading.
Gentle threshing and efficient separating with wide-body X Series dual separator
Separate every grain
The wide-body concept produces a thinner crop mat as it can spread over a wider surface area. This reduces the crop pressure for easier and more efficient threshing and separation.
Efficiency on a new level

A dual-rotor design was adopted for good reasons. Huge know-how has been gained over many years on how to optimise performance in the narrow body S700 Combine. This design is simply doubled and put into the wide body X9 Combine. Rotors also produce superior grain quality and offer better crop versatility and accessibility than other concepts. For the X9, a configuration was chosen with two longer rotors positioned in a wide channel to create a massive threshing and separation area. This has allowed the combine to set new performance levels in the industry of 100 t/hr with no more than 1 percent losses.
- 270-degree even loading
- 4.0-m² (43.05-sq ft) effective threshing area
- 25.2-m² (271.25-sq ft) effective separating area
The design of the three-in-one rotors is the secret to the X9 Combine’s highly efficient separating performance. Its combination of low power feeding, a gentle pull-and-release threshing action, and energy-efficient centrifugal separating is unbeatable.
Gentle crop-on-crop threshing

The crop passes 1.6 m² (1.6 sq ft) of threshing concave area two and a half times, adding up to 4.0 m² (43.05 sq ft) of pure threshing capacity. This means the concave settings don't have to be tightly set, resulting in less aggressive threshing. It also reduces contact between grain and metal which minimises broken kernels. This not only leads to better grain and straw quality, but it is also more energy efficient as the crop density is lower.
Efficient separating

The separating elements create a combing action to pull the crop apart. They are also staggered in a way that moves the crop towards the discharge beater as the rotor turns. The crop rotates an average of seven times in the separation area before reaching the discharge beater. This exposes it to 25.2 m² (271.25 sq ft) of effective separation area.
The rotor also creates a highly energy-efficient centrifugal separating effect. Its large, 610-mm (24-in.) diameter produces a bigger separating effect without needing the energy-intensive high speeds of smaller diameter rotors.
Thorough cleaning from the large, high-performance cleaning shoe
Cleans every grain

The massive 7-m² (75.3-sq ft) cleaning shoe delivers high-quality grain with minimum losses. The most efficient way to clean the crop with minimum loss is pure size. The body design means the X9 Combine can accommodate a wide and long cleaning shoe. It's capable of handling well in excess of 100 t/h. Extensive testing in all crop types also showed it is less sensitive to adjustment errors and does not require constant tweaking to get the optimum performance.
- 7.0-m² (75.3-sq ft) cleaning shoe area
- Four high performance turbine fans
- Six loss sensors
Actively threshed tailings
The X9 Combine is also equipped with an active tailings system. This is a major performance enhancing addition that separately threshes the tailings. It uses smooth rubber threshing elements to minimise grain damage. Acting as a mini threshing system with its own drum and concave, it reduces the load on the main rotors. This frees up capacity for more crop throughput because the tailings are not being returned to the rotors to undergo separation. That means the concaves can be opened wider which lowers the power requirement and improves fuel efficiency.
Increase cleaning system performance on hills with slope compensation
No compromises on hills and slopes

The Active Terrain Adjustment™ system automatically adjusts all the important cleaning shoe settings (fan speed, chaffer, and sieve). The software also has an industry-exclusive crop matrix which makes specific adjustments for the type of crop that is being harvested. For instance, rapeseed is particularly sensitive to fan speed changes, so the system adjusts the chaffer and sieve settings first before adjusting the fan speed.
Uphill slopes
When going uphill, both the chaffer and sieve are opened while the fan speed is reduced to keep grain from being lost through the rear. This increases the cleaning system performance by up to 50 percent on inclines of up to 16 degrees.
Downhill slopes
On downhill slopes, the chaffer and sieve close while the fan speed increases to keep grain from pushing towards the front of the machine. This reduces the volume of tailings by as much as 50 percent, resulting in a cleaner grain tank sample.
Sidehill compensation
The cleaning shoe is equipped with six divider plates on the preparation pan and chaffer. These ensure material is evenly delivered across the entire width of the cleaning shoe, and there is no chance of it sliding or moving to one side.
Once the material reaches the cleaning shoe, the real advantages of its longer length over other concepts becomes clear. This gives the grain more opportunity to fall through the chaffer and sieve without overloading one side of the shoe.
Less than 1 percent broken kernels with X9 Combine design innovations
Maximum quality, minimum losses
Independent research* has shown that if a combine has 1 percent broken kernels in the tank, a further 1 percent of broken kernels will have been lost via the cleaning shoe. The X9 Combine is designed to minimise these losses, increasing your profit per hectare.
*NOTE: Feiffer Consult, Harvest Poll, 2005 www.feiffer-consult.de
Several design innovations contribute to the exceptional grain quality: the low rpm of the large-diameter dual rotors; threshing elements and separating tines as well as rubber threshing elements on the active tailings return system which reduce grain to metal contact; crop-on-crop threshing; and a streamlined crop flow with no sharp edges.
Combine Advisor™ technology

Combine Advisor automatically guarantees consistent output whatever the conditions. Digital cameras located in the clean grain and tailings elevators continuously measure grain quality and the amount of foreign material, making real-time and automatic adjustments to maintain the pre-set levels with no operator input required.
Combine Advisor is linked directly to the HarvestSmart™ system which controls the combine's harvest speed. If the settings cannot deliver the desired output, the combine's speed is lowered. If conditions improve, the combine's speed is increased.
Residue management with chopper options and patented knife design
Destroys everything
Depending on the required chopping intensity, there’s a choice of a high-performance 124-knife premium chopper operating at 3000 rpm or a 68-knife deluxe chopper operating at 2400 rpm.
Fast conversion times

The chopper can be moved electrically from transport to working position. When converting to corn, there is no need to change knives and engage a corn cob deflector. All you do is lower the chopper speed to 1600 rpm using the chopper gearcase lever.
- 124 knives
- 20 kW (27-PS, 26.6-hp) maximum power saving
- 15-m (49.2-ft) spread
Low-energy knife design

The patented chopper knife design reduces power consumption by up to 20 kW (27 PS, 26.6 hp) compared to standard wing knives. The secret to its performance is the small dimples on its surface. Similar to the dimples on a golf ball, they reduce air resistance over the surface of the knives.
Automatic wind compensation

AutoSwap automatically changes the spreading direction of the chopper to compensate for side wind based on global positioning system (GPS) data. There’s no need to press the swap button at the headland, and there’s no chance of forgetting to change direction and running with the wrong settings.
Large footprint and durable design from John Deere tracks
Reduced soil compaction
John Deere’s latest tracks with an extra-large footprint and exceptional grip will keep you harvesting in muddy conditions.
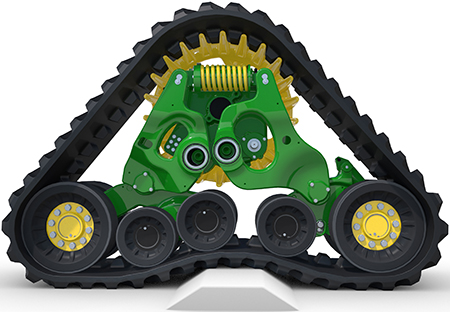
In customer tests against a leading competitor, the latest track design scored substantially higher ratings on all key criteria: ride quality, noise, and vibration. The triangular profile creates a climb-out-of-mud effect, and the longer length gives a larger footprint without adding to the overall combine width. This reduces soil compaction and avoids the need for deep tillage, saving costs all year round.
- 20 percent smoother ride
- 30 percent larger footprint
- 50 percent longer track life
Built to last
The tracks’ progressive suspension design is patented technology, unique to John Deere. When you add to this the five-pivot point technology, the tracks have unbeatable terrain following capability. This gives a very smooth ride, even at speeds up to 40 km/h (25 mph). The single-piece moulding and tread pattern also reduce friction, generating 50 percent less heat. This significantly reduces wear and extends the working life. Internal tests with a leading competitor showed 50 percent less wear.
More torque and less fuel with ProDrive™ XL transmission
Express transfers
John Deere already has a strong reputation for its tractor transmissions, and you can enjoy that same reliability and seamless shifting from 0 to 40 km/h (0 to 25 mph) on the X9 Combine.
Fuel-efficient dual motors

The infinitely variable ProDrive XL transmission is standard on the X9 Combine, making it very easy for anyone to drive. It's the next generation of the well-known ProDrive transmission, offering 30 percent more torque throughout the entire speed range.
ProDrive XL uses two smaller motors instead of a larger single motor. When the combine is driven above 20 km/h (12.4 mph), one of the motors disengages which improves fuel economy by up to 30 percent. What’s more, it’s a lot quieter than traditional hydrostatic transmissions.
- 40-km/h (25-mph) road speed
- 30 percent more torque
- 30 percent fuel saving
Four-wheel drive (4WD) and differential lock for maximum traction
The optional 4WD ensures you'll still be harvesting when others have stopped. Every X9 Combine is also equipped with a front axle differential lock as standard. If you hit really tough conditions, all you have to do is push a button on the CommandARM™ console to engage.
Excellent fuel efficiency on X9 Combines
Engineered for fuel economy

Every single component is designed for efficiency, bringing a massive 86 kW (116.9 PS, 115.3 hp) in energy savings. Add to this a lower driveline top speed of 1900 rpm, and the X9 delivers incredible fuel economy for its throughput.
- Lightweight components
- Three-speed rotor drive
- Self-lubricating pulleys
- High-efficient crop flow
- High-efficient cooling
- Large diameter pulleys
- Switchable motor drives
- Golf ball effect of updated chopper knife design
High-power and fuel-efficient updated engines
Energy-efficient Harvest Motion
Welcome to Harvest Motion: a combination of a state-of-the-art engine with optimised performance characteristics, low fuel consumption at reduced rpm, and perfect synchronisation with an energy-efficient crop flow.
Updated engine technology

Engineers developed updated engines for X9 Combines following similar innovations used in the automotive industry, where the trend is towards engines with smaller displacements, higher power density, and improved fuel efficiency. The target set was a 20 percent improvement in fuel economy per harvested ton.
- 515-kW (700-PS, 690.4-hp) maximum power
- 20 percent more fuel efficient
- 27 kW (37 PS, 36.5 hp) saved
All the core components are completely new designs, including the engine head, turbocharger, and exhaust gas recirculation (EGR) system. Together, these modifications have a big impact on the energy efficiency of the entire power pack. They save up to 27 kW (37 PS, 36.5 hp) that would normally be lost on these core components.
Lower rpm and lower cost
Efficient machines are simply good business. The X9 driveline was specifically designed to deliver optimal crop flow exactly when the engine is operating in its energy efficient sweet spot. That's Harvest Motion.
Power output increases by 65 kW (88 PS, 86.8 hp) between 1700 and 1900 rpm. The characteristics of the engine torque curve means there is also tremendous reserve capacity, even at low rpm. The torque increases to an impressive 3000 Nm (2212.7 lb-ft) at 1500 rpm. It’s why this engine practically never dies, no matter how hard it’s pushed. At the same time, the low rpm helps X9 Combines deliver impressive fuel economy, as less revolutions simply mean less fuel is burnt. It all adds up to higher throughput and lower fuel cost per ton.
On the road, the X9 is just as economical. The engine speed management reduces rpm to 1700.
Increased uptime with comprehensive support from John Deere
Caring for you day and night
John Deere has developed a comprehensive range of maintenance services for every eventuality. You can be sure that you can keep harvesting whatever happens.

John Deere’s solution is a combination of highly trained specialist dealer technicians and wireless connectivity for remote monitoring of onboard sensors. As one of the world's largest combine harvester manufacturers, John Deere has thousands of connected machines running in the field. This provides valuable data on component reliability, which allows John Deere to move beyond traditional preventative and corrective maintenance to provide a new level of service: predictive maintenance, otherwise known as Expert Alerts.
- Preventative maintenance - scheduled routine maintenance to keep your combine running efficiently
- Corrective maintenance - fixing an issue as quickly as possible with 24/7 parts delivery, PowerGard™ Protection/Protection Plus, Service ADVISOR™ Remote, and Remote Display Access (RDA)
- Predictive maintenance - identifying potential issues and replacing parts before they fail with Expert Alerts, John Deere Connected Support™, and remote machine monitoring
Always keep harvesting with 24/7 parts delivery
Backup combine

John Deere’s Harvest Promise package is included as standard with every new X9 Combine: you can get any parts you need within 24 hours of placing your order. If the parts don’t come and your X9 can’t harvest, your dealer will provide you with a backup machine* of a similar size.
- Expert Check – a comprehensive pre-season check by certified technicians that covers everything from wear parts to software updates
- Harvesting professionals – factory-trained experts are on hand throughout the harvesting season to give you help and advice
- Backup machine – annual pre-season Expert Check required by your John Deere dealer and valid on combines up to 7 years old
- 24-hour parts promise – the best parts logistics network in the agricultural business, delivering 97 percent of orders within 24 hours
- Driver training – refresher training so drivers are fully up to speed on combine optimisation from day one of the harvesting season
*NOTE: A backup machine is available for any John Deere combine harvester up to 7 years old at participating dealers. To qualify, it must be maintained in accordance with the operator's manual and undergo a pre-season Expert Check with any recommended repairs carried out.
Comfort and control in the quiet X9 Combine cab
First-class cab

There is nothing quite like the X9 Combine cab. The reassuring sound of the electric door closer, the silence, and the space ‒ its design reflects the changing role of the operator, from a driver or technician to a control systems and data management expert.
- 3.68 m³ (130 cu ft) of space
- 25.5-L (0.9-cu ft) refrigerator
- 10 USB and 12-V outlets
The panoramic windows with thin support pillars give a clear view over the feeder house, the ends of the header, and to the tip of the unloading auger. The super quiet interior lets you make hands-free calls, listen to music, and use it as a productive workspace.
The advanced air conditioning and Ultimate Seat option with massage function make it a relaxing environment, even in the most intense harvesting situations. Once you’ve experienced it, nothing else feels this good.
Useful storage

You’ll find plenty of places to store your personal items and keep the cab clean and tidy. From inside the armrest to behind the seat and more, there's a place to store everything from smartphones and keys to bulkier items. There are also cup holders for hot drinks and water bottles.
Quality infotainment

You can connect your mobile devices via Bluetooth® wireless to the infotainment system. Listen to the radio, stream your favourite music or podcasts, and safely make hands-free calls without taking your eyes off the main controls. Communication is seamless thanks to the quiet cab and excellent sound quality.
Large fridge

Unlike a simple cool box that needs pre-chilled items, the onboard fridge works just like the one you have at home and cools down warm items. The 25.5-L (0.9-cu ft) capacity is ample for a long day of harvesting.
Dust-sealing doors

As you close the door, an electric motor automatically pulls it shut. This ensures the perfect seal and prevents dust and debris from entering the cab. The interior is also pressurised, so when you open the door, dust and debris is automatically blown away from the cab.
Handy power

There are plenty of 12-V and USB charging points conveniently positioned so you won’t have to worry about bringing additional adapters. They’re particularly useful if you want to connect additional screens or charge your mobile devices.
Five-star luxury

Choosing the ActiveSeat II with leather seat cover and leather steering wheel option is an investment you will never regret. When working long hours in tough harvesting conditions, a high-quality operator environment is essential. It’s also a powerful incentive to attract the best talent. Once experienced, you’ll never want to sit on another combine seat again.
- All-around cooling
- Exclusive active suspension (ActiveSeat II)
- Lower operator stress
- Perfect body support
Bluetooth is a trademark of Bluetooth SIG, Inc.
Customization from the easy-to-use CommandPRO™ control lever
Customisable control

The CommandPRO lever was inspired by handheld games controllers and John Deere operators. You wanted more programmable features, easy-to-use fingertip control, and exceptional comfort for long harvest days.
You can enjoy more functions than ever on your combine controller. Programmable buttons that can be set for different operators and an ergonomic design that fits the hand like a glove makes operating an X9 Combine a breeze.
Easy to program
If you have different operators, they will love being able to store their own individual settings and call them up when it’s their turn to drive. It takes just a few seconds on the touchscreen display to programme the CommandPRO with draper belt speed, reel height, unloading auger folding, chopping spread direction, feeder house tilt, and much more.
Start harvesting sooner with quick setup and navigation on the intuitive displays
Logical menus and customisable screens

A major design principle for the X9 Combine was to make the operation as intuitive as possible. This was to ensure any operator can quickly get acquainted with the main functions of the combine, learn the details on the go, and provide easy-to-use automation support wherever possible.
Fast navigation
Logical menus and a shortcut bar make navigating easy. For instance, use Quick Line to record an AB line at the press of a single button.
Quick set up
The Settings Manager lets you store setups from previous jobs such as concave clearance and drum speed. You can then call them up in seconds and start harvesting almost immediately.
Real-time data transfer
The X9 is constantly collecting data and transmitting it in real-time to your own account in the cloud-based Operations Center at MyJohnDeere.com. Securely stored, it’s accessible from any device.
Customisable screens
The standard menus were developed with producers during a field test programme, but you can also easily customise them to suit your needs. You simply drag and drop the menus like a smartphone and store them for future use.
Integrated camera
You can view up to four separate camera inputs on the display. These can be set up so they are automatically triggered to appear when they are needed (e.g., a camera feed from the auger when unloading).
Optional additional monitor
An additional screen can be used for precision ag applications while leaving the primary display for the main combine controls, giving you an even better view of everything.
Excellent visibility with bright, long-lasting lighting
24/7 harvesting

The X9 Combine makes extensive use of the latest LED lighting technology with more visibility, easier unloading, and safer road transport.
LED lighting has many advantages over traditional lighting. Bulbs last longer – with a lifetime of more than 20,000 hours, you won’t need to carry any spares. They are also more efficient and brighter for better visibility.
Customise to your operation
You can program different lighting configurations via the Gen 4 display to suit your specific harvesting operation.
Apart from being an appealing design, the end panel lights are a useful safety feature for unloading at night. The tractor operator can clearly see the end of the header and make sure the grain trailer is fully aligned.
Integrated lights under the side panels make inspection at night much easier. There’s no need for flashlights, leaving both hands free to access components.
Unload quickly with the harvest logistics of the large grain tank
High-speed grain handling
The combination of a large 16,200-L (460-bu) grain tank and 186-L/s (5.3 bu/sec) unloading speed with 40 kW (54 PS, 53.3 hp) extra unloading power allows you to focus on harvesting. All it takes is just 100 seconds to unload 13 tonnes of grain.
Built for tough conditions

The grain handling system features a heavy-duty, belt-driven design that performs equally well in high yielding crops and wet conditions. Tool-free adjustment of the cross auger cover plate in the grain tank also allows the load rate to be adjusted for different crops and conditions.
The engine’s electronic management system provides a power boost of up to 40 kW (54 PS, 53.3 hp) when unloading so there’s no need to slow your harvesting down.
See better and load more grain with the innovative auger design
More control and easier to use

The auger swings up to 106 degrees, giving you an excellent view when unloading. You can also watch the grain unloading on the Gen 4 display via a video feed from an optional wireless camera on the auger.
Reduced risk of damage
The auger has a clearance of up to 5.1 m (16.7 ft) between the unloading boot and the ground so there’s less risk of damage with high-sided trailers. It also has a mechanical latch in transport mode which prevents any movement when driving over rough surfaces.
Space-saving design
The X9 is equipped with a folding auger as standard. It makes storage and manoeuvring in tight spaces easier and is useful for road transport.
Low stress operation
The large diameter of the auger means it can transport massive amounts of grain at lower rpm. Apart from less wear and tear, it reduces potential grain damage due to less grain-on-metal contact.
Cross auger delay

The entire auger can be emptied automatically before shut-off. Simply press the unloading button to start the process. Press the button again, and the grain tank cross augers disengage while the unloading auger continues for another 3 seconds to ensure it's completely empty. To stop the entire system immediately, double click the unloading button; this is a handy feature when you want to top off the grain cart or trailer.
Adjustable spout
With the adjustable spout, you can precisely direct the grain flow by up to 1 m (3.3 ft) to fully utilise the available space in the trailer or grain cart. When the auger moves to the park position, the adjustable spout moves up and away for improved clearance.
Increase harvesting efficiency by controlling combine unloading with Machine Sync
Stress-free unloading

Machine Sync is a powerful machine-to-machine communications application that allows you to connect multiple machines and operate them together.
Remotely check combine grain fill level

Machine Sync allows the grain trailer operator to view the location of all the combines in their network. They can see the direction of travel and grain tank fill level and can decide which combine to unload next. Alternatively, the combine operator can request a tractor for unloading at the touch of a button. This ensures optimised routing for grain trailers, saving time and fuel and reducing soil compaction.
Combine operator takes control of unloading tractor

As the tractor pulling the grain trailer arrives near the combine, the operator activates Machine Sync. The system automatically takes control of the tractor’s steering and speed. The tractor operator can then take their hands off the steering wheel.
Combine operator steers tractor

The combine operator can now control the position of the tractor relative to the combine. If the combine changes direction or speed, the tractor also changes direction or speed - both are synced in perfect harmony.
Operator releases control of unloading tractor

When the trailer is fully loaded, the tractor operator can take over control simply by turning the steering wheel. Alternatively, the combine operator can also stop the synchronisation from their display.
Work faster and smarter with automatic precision self-driving
AutoTrac™ guidance

Developed and refined over more than 20 years, AutoTrac hands-free guidance automatically ensures the full cutting width of the header is used with every pass hour after hour and day or night. It's unaffected by hills, down crop, or dusty conditions. With the quick A-B line features, it's set up in seconds.
- Start harvesting faster using AutoTrac online
- Share guidance lines with multiple machines in the field
- Integrated StarFire™ 6000 Receiver uses up to three correction signals
What's more, AutoTrac also shows where other combines have already been in the field and lets you share guidance lines between other machines. You can also work in beds to optimise field logistics.
Always stay in the right row
If you’re harvesting corn planted in curves, blown down by the wind, or simply in a field with uneven row spacing, AutoTrac RowSense™ will keep you on track. Its advanced technology uses feeder data gathered from both row sensors on the header and satellite positioning from the StarFire receiver to follow the rows exactly.
Improve harvest productivity with automated systems
Best performance guaranteed

The X9 Combine has a range of adaptive automation tools that ensure every operator’s productivity is as good as the best operators. Easy to set up, they not only help choose the optimum settings, they automatically maintain them.
Research amongst a wide range of operators showed that, on average, the utilisation of the installed capacity can be increased by up to 20 percent*. The good news is the X9 is equipped with adaptive automation tools and technology to do it for you.
*NOTE: From ‘dlz agrarmagazin’ 6/2017
Optimise Performance feature
The Optimise Performance feature helps optimise the combine setup. The operator simply follows an interactive menu which gives recommendations for settings based on harvest priorities (losses, grain quality – broken kernels and dirt level, and straw quality). It even suggests external adjustments to the combine. The goal is to tell the combine the desired output: loss level, grain and straw quality, and grain tank cleanliness.
Combine Advisor™ technology

Once the machine has calculated the output required by the farm operation, Combine Advisor takes over. It automatically makes adjustments to maintain the desired quality of work and tries to maximise the throughput. No operator input is required, taking away additional stress and ensuring optimum harvesting all day long.
HarvestSmart™ system
This automatic speed management system lets you run your combine close to its capacity or loss limit. It takes multiple calibration points at different speeds and throughput levels across the typical working range. This greatly improves sensitivity to different conditions and delivers precise control. To ensure performance is maintained, HarvestSmart will automatically slow the combine down if Combine Advisor can no longer make adjustments to deliver the desired outputs. In turn, HarvestSmart will automatically increase the combine’s speed if conditions and settings allow it.
Save time by recording accurate data with the ActiveYield™ monitoring system
High-quality sensors for easier calibration and more accurate data

Moisture and yield sensors are well established tools to help monitor performance of different crop varieties, but the ActiveYield system on the X9 Combine offers even higher accuracy and improved harvest management.
- Save time - no need to interrupt the harvesting chain for regular weighing in of different crops and conditions
- Improves yield mapping accuracy
ActiveYield features three precision sensors in the grain tank that automatically measure the change in weight as the grain tank fills. The system compares the measurement from the tank sensors to those from the yield and moisture sensors to accurately calibrate the yield sensor. You no longer have to carry out time-consuming manual calibrations and double weighing of trailers at a weigh bridge to get accurate yield measurement data. This improves harvest logistics as grain trailers spend less time travelling to the silo. It also eliminates the risk for errors in the yield maps as there is no need to enter calibration data into the system manually.
View, send, and manage data from anywhere with MyJohnDeere.com
Harvest in the cloud

The X9 Combine harvests tons of valuable data from every hectare. This data has an increasing role in improving yields, automating documentation and maximising profitability.
- Local dealer support
- Open data sharing
- Secure data access
- Bespoke services
- More than 150 software partners
- Secure storage
Through JDLink™ system, field and machine data are automatically transmitted to John Deere’s secure servers in the cloud. It can be viewed in the John Deere Operations Center in your MyJohnDeere.com account, or via mobile apps. The Operations Center is compatible with data from a growing number of other agricultural machinery brands and an increasing network of independent agricultural service and software providers. This gives you a level of management control that is unrivalled in the agricultural industry.
Manage your operation from anywhere

Mobile apps and cloud-based storage allow you to manage your harvest from any device with any brand of machine.
The harvest season is always unpredictable with sudden changes in the weather and different crop cycles. That’s why you need the maximum possible flexibility. The Operations Center can be accessed from any device in any location, so it doesn’t matter if you’re in the office or out in the field, you have a clear view of your entire operation in real time.
What’s more, mobile apps let you send job details or remotely adjust combine settings in moments. It gives you the freedom to maximise the efficiency of your harvest logistics and your grain yields on your own terms.